For decades, ultrasonic measurement technology has been the cornerstone of level measurement across various industries, including water utilities and industrial sectors worldwide. Initially, ultrasonic systems faced challenges like “false echoes” caused by signals reflecting off surrounding hard structures, such as pipes or walls, which interfered with accurate measurements. However, advancements in digital signal processing and technology have significantly enhanced the reliability and versatility of ultrasonic devices. Today, they are not just level sensors but sophisticated tools for pump control, differential measurement, and more.
How Does Ultrasonic Measurement Work?
Ultrasonic sensors operate by sending out a pulse of sound using a piezoelectric crystal. When the sound wave encounters an object, it reflects back, and the returning echo is detected by the sensor. The time taken for the echo to return is directly proportional to the distance of the object. Modern ultrasonic systems can filter out echoes from stationary objects within the measurement path, allowing them to focus on the true target. The non-contact nature of ultrasonic technology ensures no moving parts, reducing maintenance needs, making it an ideal choice for a wide range of applications.
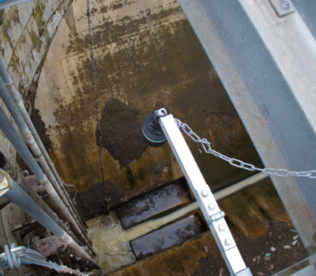
The Myths Surrounding Radar Technology as a Superior Alternative
In recent years, there has been a growing perception that radar-based measurement technologies are superior to ultrasonic methods. While radar systems—particularly those using Frequency Modulated Continuous Wave (FMCW) technology—are more suitable for specific applications, ultrasonic systems still solve about 95% of level measurement challenges. The latest ultrasonic devices come with high acoustic power, allowing them to provide reliable measurements even in turbulent or foamy environments.
Key Benefits of Ultrasonic Measurement
- Proven Reliability: Ultrasonic technology has a long history and is well-understood, making it a go-to choice for accurate and consistent level measurements.
- Energy Efficiency: Modern ultrasonic systems can operate on low power, making them suitable for remote locations and applications where energy efficiency is critical. Advances in power management have led to battery-operated ultrasonic devices that can last for years, reducing operational costs.
- Versatility: Ultrasonic sensors are not just limited to level measurements; they are also effective for pump control, open channel flow measurement, and more. This adaptability makes them invaluable across various industries.
- Minimal Maintenance: With no moving parts, ultrasonic systems require little to no maintenance, enhancing their longevity and reliability.
Understanding Radar Measurement Technology
Radar measurement technology, particularly non-contact types, works by emitting radiofrequency waves and measuring the time it takes for these waves to return after hitting a target. There are two main types of radar measurement: pulsed and FMCW. While radar can offer advantages in specific conditions—such as measuring through plastic walls or in high-temperature environments—it also comes with its own set of challenges, especially when measuring materials with low dielectric constants.
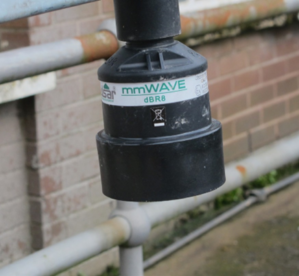
When to Consider Radar Over Ultrasonic Measurement
While ultrasonic remains a versatile and robust choice for most applications, radar technology may be more suitable in the following scenarios:
- Longer Range Applications: Radar can provide better accuracy over longer distances, particularly in open channels.
- High-Temperature Environments: When measuring hot surfaces, the speed of sound in ultrasonic devices may vary, affecting accuracy. Radar is less impacted by temperature changes.
- High Electrical Noise Environments: Radar can handle environments with high acoustic noise more effectively than some ultrasonic systems.
- Foamy Surfaces: While ultrasonic devices with high acoustic power can measure through foam, radar generally offers more stability in such conditions.
- Chemical Dosing Plants: Radar can penetrate plastic walls, making it ideal for measuring levels in Intermediate Bulk Containers (IBCs) commonly used in chemical dosing.
- Biogas Digesters: The methane-rich and pressurized environments of biogas digesters can pose challenges for ultrasonic sensors. Radar can provide more reliable measurements under these conditions.
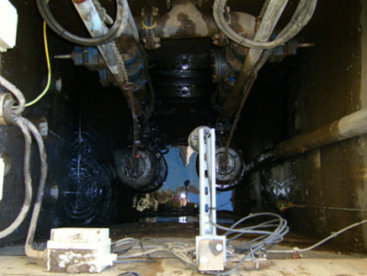
The Best of Both Worlds: A Flexible Control System
To ensure the flexibility of using either technology, investing in a control system compatible with both ultrasonic and radar sensors is wise. This allows you to switch technologies easily if application requirements change, avoiding additional costs for new control systems or extensive retraining for engineers.
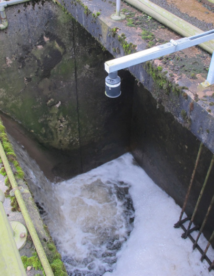
Conclusion
Both ultrasonic and radar technologies have their strengths and limitations. Ultrasonic measurement remains a reliable and cost-effective solution for most applications, while radar technology is beneficial in specific conditions where ultrasonic systems may face limitations. Choosing a control system that supports both technologies ensures versatility and prepares your operations for future challenges.